ITMA 2023 showcased the most recent developments within the still-growing digital printing area.
By Dr. Lisa P. Chapman, Technical Editor; and Kerry McGuire King
ITMA 2023, aptly named “Remodeling the World of Textiles”, centered on sustainability achieved in three innovation areas which are instantly associated to digital printing — Superior Materials, Synthetic Intelligence and Automation. This yr was the biggest iteration of the present with greater than 111,000 attendees from 143 nations (2019: 105,000) 1,709 exhibitors from 47 nations (2019: 1,717), and 200,000 sq. meters of exhibition house (2019: 114,500 sq. meters). Digital printing was once more closely featured at ITMA 2023, with a complete corridor dedicated to this expertise. The digital print market grew considerably for the reason that final ITMA. There was a slowdown through the pandemic, however now there’s a return to a progress market.
ITMA 2015 noticed a transformative breakthrough with the event of single cross printers, able to printing at speeds as much as 70 meters per minute (m/min). Surprisingly, these high-speed printers weren’t featured as prominently at ITMA 2023. Relatively, the emphasis was on the optimization and maturation of scan sort printers with a deal with sustainability, in addition to optimization of the printing course of to enhance high quality and scale back colorants, chemical compounds and time. Scan sort printers, whereas nonetheless not as quick as single cross printers, at the moment are a lot quicker than what was proven at ITMA 2019, reaching speeds of 15 to twenty linear yards per minute. The elevated pace of scan sort printers is achieved by stacking print heads. Though slower, scan sort printers additionally provide higher flexibility, and in some cases greater high quality. The excessive pace of single cross printers means roughly 20 p.c of designs can’t be achieved, significantly these prints the place extra saturated, bigger stable print areas are required. Scan sort printers are cheaper and take up much less flooring house and so it’s attainable to have a number of on the manufacturing unit flooring printing utilizing completely different colorants on quite a lot of substrates. Scanning applied sciences provide manufacturing flexibility and redundancy, which is essential for print on demand environments the place ultra-short run printing contains fast turns throughout quite a lot of supplies and product sorts.
Scanning options provide the flexibility to scale manufacturing over time by the addition of machines and the flexibility to “step up” to the subsequent machine stage. This can be a technique provided by quite a few distributors.
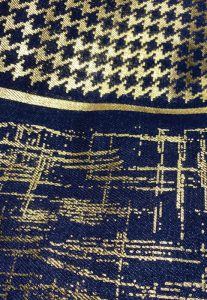
Roll-To-Roll/Direct-To-Cloth Printers
At ITMA, Japan-based Epson showcased the Monna Lisa sequence —broadly thought of to be one of many premium applied sciences for the high-est decision and highest-quality prints — together with the ML 8000, 16000, 32000 and 64000 machines for which the mannequin quantity corresponds to the variety of printheads and subsequently throughput functionality. Fashions and capabilities embody:
- ML 8000, which prints with a set of reactive and acid dyes, referred to as REACID, for fiber blended substrates, or for extra flexibility if for instance, a buyer wished to print substrates suitable with acid for one print run and reactive for an additional.
- ML 13000, which presents inline pre- and post-treatments with pigment inks. The pretreatment liquid, ejected by one of many print-heads, jets a surfactant agent to tug the ink to the floor of the material, which helps to make the print extra colourful. One other print-head jets a binder for elevated fastness properties, whereas one other printhead jets a softener to enhance the hand of the material.
- ML 16000 hybrid, which mixes piezo-electric printheads with microvalves. The printheads jet pigment colorant and the microvalves are in a position to jet paste for results akin to metallic and white pigmented coloration.
- ML 3200, which has a printable width of 340 centimeters and 32 printheads. This printer may be configured to print two items of material concurrently, thus growing productiveness and lowering vitality and useful resource consumption.
Italy-based EFI Reggiani confirmed the chance to step up in machine width with its Hyper mannequin out there as a 1.8-, 2.4-, or 3.4-meter-wide machine. Geared up with 72 printheads and ink recirculation as much as the nozzle plate, it might print two cross, manufacturing high quality at speeds as much as 13 linear m/min on a 1.5-meter-wide roll. The widest machine additionally presents dual-roll functionality to print two completely different, narrower substrates without delay at throughput speeds of as much as 20 m/minute. That is an fascinating idea, proven by Italy-based Durst on the final ITMA present, which requires particular machine and software program engineering.
Italy-based Dover Industries Italy (DII) (MS Printing Options & JK Group manufacturers), additionally featured scaling alternatives inside its scanning line. On the prime finish, the Mini Lario has been upgraded and now has eight rows with as much as eight heads per row and may print at a pace of 1,000 meters per hour. This is without doubt one of the quickest scan sort printers in the marketplace. DII (MS & JK manufacturers) reviews that the Mini Lario may be exactly coloration matched to manufacturing on the Lario to allow longer manufacturing runs of the identical design and colorway ought to the necessity come up.
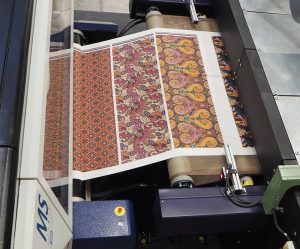
As well as, DII (MS & JK manufacturers) confirmed the reengineered JP7 machine and system that considerably improves the sustainability of all the printing course of. The middle of this optimized, sustainable printing system is Digistar Pigment 4K, a patent pending colorant set that eliminates pretreatment, thereby lowering chemical and water utilization, in addition to time and value. The printer additionally features a new zero-wastewater recirculation system that reduces as much as 90 p.c of water waste usually generated in a 40-hour working cycle. To additional optimize a sustainable printing course of, a brand new ink recirculation system from DII (MS & JK manufacturers) prevents nozzle blocking, which is a main explanation for print material defects that results in material and colorant wastage. Gradus, its in-line drying system, ensures minimal vitality consumption; and since the modular system permits curing and drying multi function, carbon dioxide emissions are diminished.
Austria-based Zimmer Austria Inc. — a producer of machines for textile and carpet ending together with digital printing methods, flat and rotary display printing, coating methods, steaming, washing and drying — showcased the Colaris3 high-performance pretreatment, digital printing and colorant methods for functions that require colorant penetration by the substrate akin to carpeting, towels, and plush or heavy automotive and residential décor materials. The Colaris sequence of printers can be utilized with quite a lot of colorants akin to reactive, disperse, acid, pigment and vat. Inline pre-and post-treatment methods may be added to enhance print high quality and improve ink penetration. The Colaris printer has 16 printheads for a bigger coloration gamut, elevated pace, or flexibility to run a number of kinds of colorants. Zimmer has added a imaginative and prescient digital camera detection system to its Colaris digital printers. The Colaris-vision I – Match Print to Lower contains particular person piece items recognition and description masking with automated computation of the print masks positioning for design customization.
Zimmer’s Colaris-vision II – Match to Print is a roll-to-roll print course of with seamless detection of a pre-imagined material adopted by a registered print. The system has an automatic distortion compensation that ensures the print is fitted exactly into the given construction on an online. The design may be fitted precisely onto the substrate regardless of of any weft misalignment or shrinkage from material preparation within the pre-print course of.
Superior Supplies
As a part of the textile business’s cur-rent deal with sustainability, distributors proceed to ramp up funding within the improvement of options that scale back water, chemical and materials waste. Digital dyeing, inline pretreatment, and pigment printing all have the potential to enhance sustainability. Particularly, pigment colorant was featured by numerous distributors. As pigment expertise matures, com-petition is growing in a manner that’s resulting in enhancements in print high quality and improvements in chemistry and utility. Additional adoption of ink recirculation methods is a contributing issue to the success of pigments and this concept was highlighted by EFI Reggiani in its Hyper system. Ink recirculation was additionally talked about by DII (MS & JK manufacturers) in regard to its redesigned JP7 expertise together with the Digistar Pigment 4K.
Built-in softening and pretreatment improvements from a number of resolution suppliers is paving the best way for higher acceptance of pigment printed material. Japan-based Kyocera Corp., a key provider of business printhead expertise to textile builders, has joined the combo with the introduction of Forearth expertise, and highlighted the flexibility to print on a broad vary of materials.
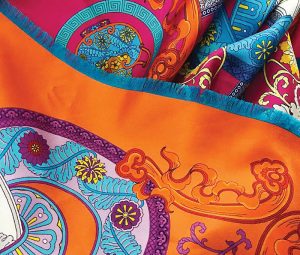
Different superior materials improvements included China-based Atexco’s double-sided printing expertise and reactive colorant that doesn’t require a submit remedy for cotton substrates.
Total, distributors illustrated the compatibility of digital printing with tricky-to-manage substrates together with knits and light-weight attire materials. This was significantly evident within the pigment printing space that had beforehand demonstrated poor material hand and coloration high quality. New pigment applied sciences are opening-up the chance for pigment printed material adoption in a broader vary of product areas and markets.
Particular Results
Advances in pigment expertise are also enabling particular impact printing. In the course of the present, Israel-based Kornit Digital Ltd. demonstrated a white pigment functionality that permits imaging on coloured grounds and when mixed with its Xdi expertise, creates a novel, raised, textural look.
Epson has taken this theme one step additional with the introduction of the ML 16000 Hybrid machine that mixes piezo-electric printheads with microvalves. The printheads jet pigment colorant whereas the microvalves jet paste to create results together with metallic and white pigmented coloration. Epson’s Genesta water-based inks assure coloration accuracy and fastness properties, whereas the particular pastes — developed and produced by Italy-based Epson Como Printing Applied sciences S.r.l.— create the particular results.
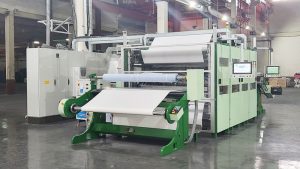
Digital Dyeing And Ending
Though pigments provide a sustainability benefit over dye-based colorants for digital printing, digital utility strategies for stable colours provide the potential for a a lot higher discount in environmental footprint. Towards that finish, England-based Alchemie Know-how’s Endeavour™ digital dyeing expertise applies liquid colorants to materials utilizing a novel non-contact high-energy jetting of nano-droplets, delivering exceptionally homogeneous coloration all through the material. This breakthrough waterless, low-carbon, digital dyeing expertise, helps dye homes in lowering prices — dramatically reducing vitality and carbon dioxide emissions by 85 p.c, water use by 95 p.c, and likewise eliminates wastewater air pollution within the dyeing course of.
Alchemie’s Novara™ digital textile ending expertise delivers sustainability with precision digital utility of purposeful finishes to textiles. Novara is a non-contact, low vitality, low chemistry, digital ending resolution that permits textile ending homes to dramatically scale back their carbon and chemical footprint and scale back prices, utilizing 85-percent much less vitality and as much as 50-percent much less chemistry in comparison with conventional strategies, in response to Alchemie. Novara delivers exactly outlined digitally managed finishes solely the place wanted. It additionally allows product improvements together with single-side ending, 2D end to form, and permits a number of finishes to be utilized to 1 material in a manner that isn’t attainable utilizing conventional strategies of immersing all the material in a chemical bathtub. As well as, Alchemie additionally presents Discovery, a laboratory system that replicates manufacturing machines, and could also be used for recipe improvement, coloration matching and new materials course of improvement.
Direct-To-Movie Printing
Shenzhen Inkbank Graphic Know-how Co. Ltd. (Inkbank), China, and Japan-based Mimaki confirmed direct-to-film (DTF) applied sciences for quickly printing clothes.
DTF printing eliminates the necessity for cloth choice, plate making and pretreatment as in comparison with the time and useful resource intensive processes required for silk display, warmth switch— rubber sheet methodology — or direct-to-garment (DTG) printing. The DTF course of is easy, and on this manner, presents a sustainability benefit. First, the design is printed instantly onto a particular switch movie which is then sprinkled with hot-melt powder. As soon as heated and dried, the switch sheet may be utilized utilizing a warmth press. The one disadvantage is the waste created as a result of a switch materials is used.
Mimaki presents the TXF150 for DTF. The PHT50 inks used for this printing course of are warmth switch water-based pigments which are OEKO-TEX licensed. The inks are secure and meet the standards for ecologically accountable textile manufacturing, in response to the corporate.
Synthetic Intelligence And Automation
As digital textile printing expertise matures and adoption of advanced, high-speed printing methods grows, resolution suppliers are also demonstrating higher funding within the creation of clever methods that ease expertise administration by enabling monitoring and optimized printer efficiency. Software program functions are aimed toward offering visibility that helps scale back machine downtime and working value, whereas minimizing waste. As clients spend money on a number of print methods to scale print capability, software program methods for automated system calibration and fleet administration additionally have gotten more and more related. Moreover, to assist drive progress in adoption, expertise suppliers are advancing digital workflow options designed to help with order administration and automation of repetitive file processing duties.
A preview of the DII (MS & JK manufacturers) System Plus Software program, a brand new print administration system, exemplifies the development towards clever methods. The expertise integrates calibration, printing software program and ink for a strong, time saving resolution. Used with DII (MS & JK manufacturers) pigments and printers, the software program system reduces calibration time by 50 p.c, will increase the colour yield by as much as 20 p.c and will increase the brightness of the colours by as much as 15 p.c. This technique’s machine studying platform, the first-of-its-kind to be commercially out there for digital printing, allows data to be gathered through the printing course of to optimize present and future print runs. This software program has the potential to get rid of print defects and scale back the quantity of colorant wanted.
DII (MS & JK manufacturers) innovation is concentrated on a extremely optimized manufacturing course of. Throughout ITMA, the corporate demonstrated the mixed significance of advancing printer {hardware} and workflow in a working setting by the use of organized plant visits to the Italy-based IMPRIMA printing mill.
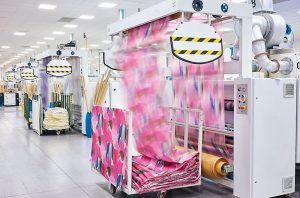
IMPRIMA is a cluster of digital print operations with the aptitude to print 35 million meters of material yearly. IMPRIMA largely serves the European luxurious market, but additionally prints for U.S.-based manufacturers akin to Walmart, Goal, Macy’s and Ralph Lauren, amongst different manufacturers.
Kornit promoted its QualiSet expertise, which is described as a wise, autonomous strategy to calibration aimed toward printhead registration, nozzle testing, compensation and coloration consistency. Paired with the beforehand launched Konnect system for monitoring printer efficiency and consumables, the corporate now presents higher skill to handle the print operation on the fleet stage. Manufacturing monitoring was additionally high-lighted by Epson for printers linked to the cloud-based PORT system, and by EFI Reggiani which confirmed the Question software program resolution that collects knowledge and allows evaluation and monitoring of printer efficiency, value and sustainability metrics akin to water and vitality consumption.
As well as, sturdy options for automating parts of the manufacturing course of to cut back or get rid of labor are rising within the digital printing sector. Kornit confirmed a completely automated DTG printing resolution that reduces labor and will increase manufacturing pace. Kornit’s Apollo DTG printer can print as much as 400 clothes per hour. Kornit’s patented wet-on-wet printing system eliminates the necessity for pretreatment. The Apollo, geared towards t-shirt printers who search a near-shoring possibility, options in-line warmth fixation, and an auto-mated loading and unloading system.
Harnessing Digital Printing Improvements
It was thrilling to see the expansion in digital printing applied sciences at ITMA 2023. Much more spectacular was seeing a few of these applied sciences efficiently applied in a manufacturing setting at IMPRIMA. Held in Milan, ITMA 2023 was situated only a quick distance from the Como area of Italy, lengthy thought of the posh printing capital of the world. This area has modified from virtually completely rotary and flat display printing to digital printing, permitting the business to service sectors past the posh market. It serves as an awesome instance of harnessing the total capabilities of digital printing improvements.
Editor’s Observe: Kerry Maguire King has greater than 25 years working within the digital printing discipline. King performed a job within the improvement of Spoonflower’s manufacturing platform, and at the moment is working as a guide whereas persevering with her training within the Ph.D. program on the Wilson School of Textiles at North Carolina State College, Raleigh, N.C.
November/December 2023